Last Updated on July 22, 2025 by PALFINGER
Our LSA service hub in Singapore offers a comprehensive service range including refurbishment and upgrades, spare parts and repair, inspection and maintenance, hook replacement, and industrial services. The location’s bread-and-butter business revolves around mandatory 5-yearly inspections in accordance with the most current regulations. The team is, of course, also more than capable of dealing with more complex, extraordinary projects.
EXTENSIVE DAMAGE POSES CHALLENGE
One of these more uncommon mandates cropped up late last year. We met up with Binu Mohanan, PALFINGER MARINE Service Manager, and Jayakanthan Peethambaram (Jana), Service Engineer and GRP Specialist, to find out more about an exciting repair job involving a severely damaged totally enclosed KISS 700 lifeboat installed on one of our customers’ larger tankers. “Initially, it was unclear whether it was even possible to repair the lifeboat. In some cases, it can be more beneficial to simply replace the boat with a newer model,” Binu recalls. “We asked an attendant to assess the damage on location in Korea, but the customer opted for sending the whole lifeboat to Singapore instead.”
A first inspection unearthed multiple severe damages concentrated around the aft section of the boat, including numerous cracks in the canopy area. “We still tried to promote the idea of replacing the lifeboat. But the customer could not afford to wait for a new model due to a three-month deadline imposed by the Maritime Port Authority (MPA) in Singapore,” Binu explains. This is the kind of difficult challenge that our Singapore team loves rising to. “After in-depth inspections and discussions, we finally agreed to take on the repair job and developed a repair plan that earned the customer an exception from the MPA,” he smiles.
WORK IN PROGRESS
The highly experienced PALFINGER MARINE experts set to work. “When we started removing components from the lifeboat, we soon realized that the damage was more extensive than initially suspected. The aft section of the canopy, for instance, was separated from both the bottom hull and inner hull liner,” Binu remembers. These new findings had a significant effect on the final two-and-a-half-month repair plan. “Once the customer agreed to the schedule, two or three experts worked continuously – and exclusively – on this project from September to November 2024.”
This is where it gets technical: “We removed all the damaged foam on the aft canopy section before grinding down and removing the compromised glass reinforced plastic (GRP) material. The section was then placed on a flat surface, secured with aluminum flat bars, and aligned using wooden frames. The GRP was laminated where needed, and the section was prepared for reinstallation,” GRP specialist Jana explains. The team also removed and ground down the damaged GRP sections in the aft hull foam chamber and strengthened the area with additional stringers. They subsequently replaced the broken aft bulkhead by a newly fabricated one.
After completing repairs on the helmsman seat, reinstalling the hook mounting tower, and concluding all other finishing work, we reinstalled the aft canopy section. “We then re-laminated the internal joint areas with GRP material and turned our attention to the remaining external repair work,” Jana says. “After returning all the removed components to their rightful place, we applied a new coat of paint. Then we conducted a successful in-house 150% load test and marina speed trials in the presence of a surveyor and owner representative,” he adds. Following a few more functional tests, we delivered the lifeboat back to the customer in November. “It looked brand new; unrecognizable given the extent of repair work we did,” Jana beams.
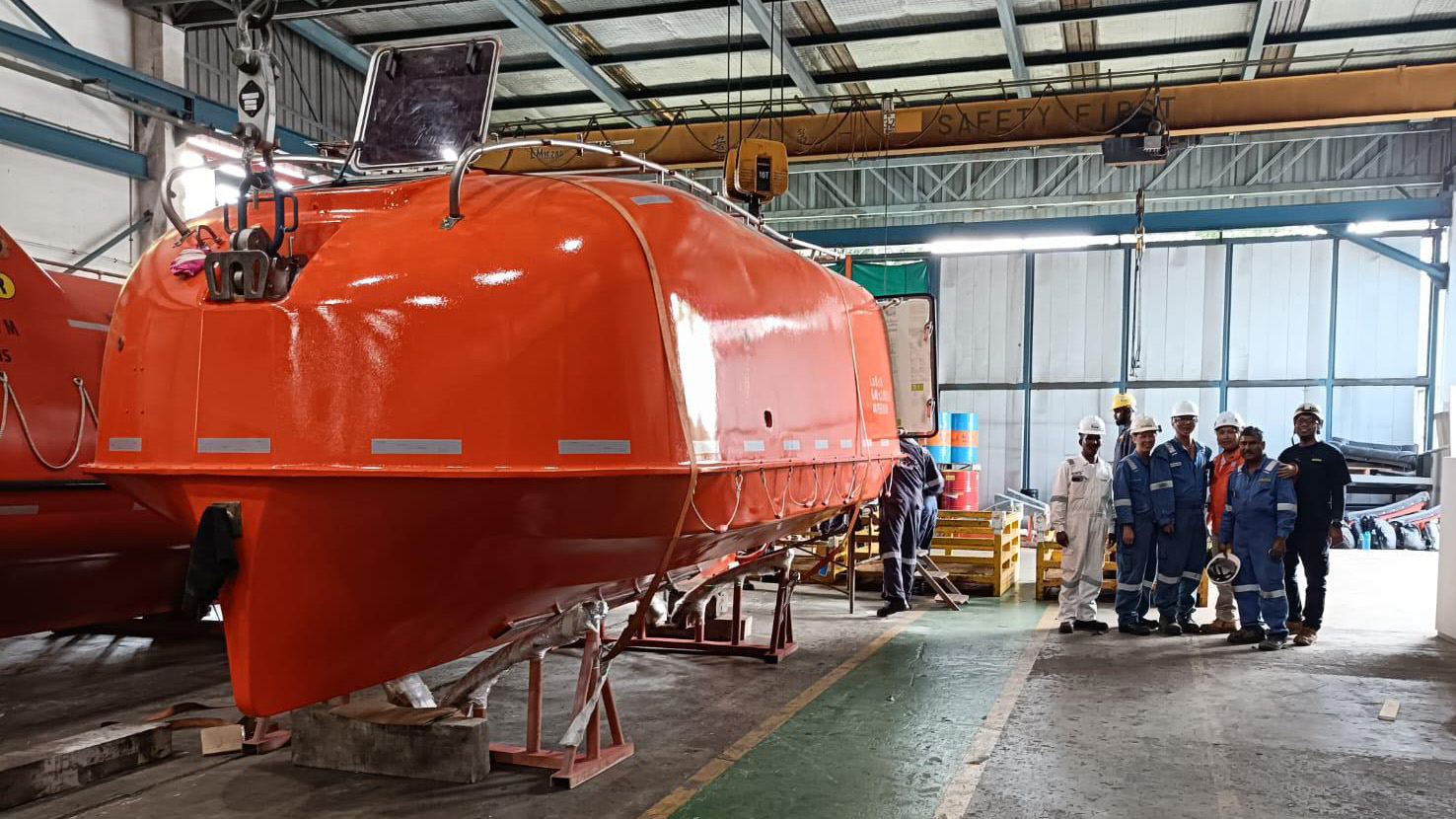
AN UNPRECEDENTED REPAIR PROJECT
So, what made this particular repair job so special? Binu is quick to answer: “We had never worked on a lifeboat with such serious damage before. It would have been easy to push for a new boat. However, we were keen to help our customer, a key account in the region, out of a sticky situation. It was a bit of a risk, because there was no guarantee that the repairs would suffice. Yet it is exactly this willingness to take risks that underlines PALFINGER MARINE’s philosophy of taking responsibility as a product innovator and reliable solution provider.”
The tight schedule was, however, not the only challenge. Ji Tang, Service Execution Director at PALFINGER MARINE, adds: “From a technical perspective, such an extensive repair job is more difficult than building a new lifeboat. It isn’t easy to maintain the same strength and weight without disturbing the gravity balance of the original vessel. You are not allowed to deviate more than 100 to 150 kilograms, as that could change the boat classification or force the customer to change the davit.” It certainly sounds like a tight rope that our experts in Singapore walked skillfully.
The strict timeline was further impacted by the fact that the Singapore office relocation was in full swing during the repair project. “Everyone was incredibly busy preparing for the grand opening of our new Singapore location in March 2025,” Ji recalls. “Despite all these external circumstances, we still managed to get the job done. It is an excellent example of what our LSA refurbishment and repair teams are capable of. And it proves to our customers that we are willing to go that extra mile for them.” This is exemplified by the recently completed spring drydock season, during which our technicians carried out similar recurring repair jobs to those in our LSA service hub in Singapore. With the added challenge of moving swiftly from one location to the next.
SERVICE EXCELLENCE DURING SPRING DRYDOCK
In the marine industry, spring and fall typically mark the cruise ship drydock season. Beyond our dedicated service team in Singapore, PALFINGER MARINE operates numerous service stations worldwide, dispatching skilled technicians to ensure smooth operations throughout the drydock season. Between January 1 and June 30 this year, PALFINGER MARINE successfully completed 430 cruise service stations across 10 countries, entailing 217 service assignments. The effort brought together professionals from 12 nations – a global team endeavor delivering exceptional results during an extended drydock season.
From routine tasks to complex overhauls, our service teams handled a wide range of work. That included annual and 5-year inspections, re-hooking, structural fiberglass repairs, hydraulic overhauls and repairs, davit steel repairs, exterior finishing, re-powering, commissioning, and much more. Many technicians moved directly from one project to the next, crossing borders with little or no downtime. Behind the scenes, our spare parts, logistics, accounting, procurement, technical and service coordination teams worked extended hours to ensure seamless execution across all regions.
These instances prove yet again that PALFINGER MARINE continues to set industry benchmarks. We are delivering innovative, reliable service solutions backed by a global team and driven by a steadfast commitment to safety and customer satisfaction.