Last Updated on May 29, 2024 by PALFINGER
After a long and tremendous effort by a team of expert engineers, PALFINGER MARINE proudly introduces a newly developed and highly sophisticated active heave compensated crane (AHC crane), which is adapted to the current needs in the market for offshore construction and subsea handling.
KEEPS THE LOAD MOTIONLESS
When operating in waves, the crane tip motion resulting from a vessel’s movements will cause great impact when landing a load on the seabed or fixed installations. This impact poses a great risk of damaging the load, the landing area or the crane structure itself. With active heave compensation technology, the influence of the waves during offshore operations can be reduced to a minimum. AHC enables the crane to keep a load motionless during landing on any fixed surface, both below and above sea level. This ability increases the time available for the operator to undertake the planned operation safely and accurately, significantly reducing the risk of damage.
What is Active Heave Compensation:
|
Since its introduction, PALFINGER MARINE’s new AHC crane design has received a very positive response in the market due to the advantageous features and competitive pricing. By the end of 2016, the first 100 tons crane with 40 meters reach was installed onboard the Norwegian platform supply vessel Vestland Cygnus.
FROM SUPPLY SHIP TO WIND FARM SERVICE VESSEL
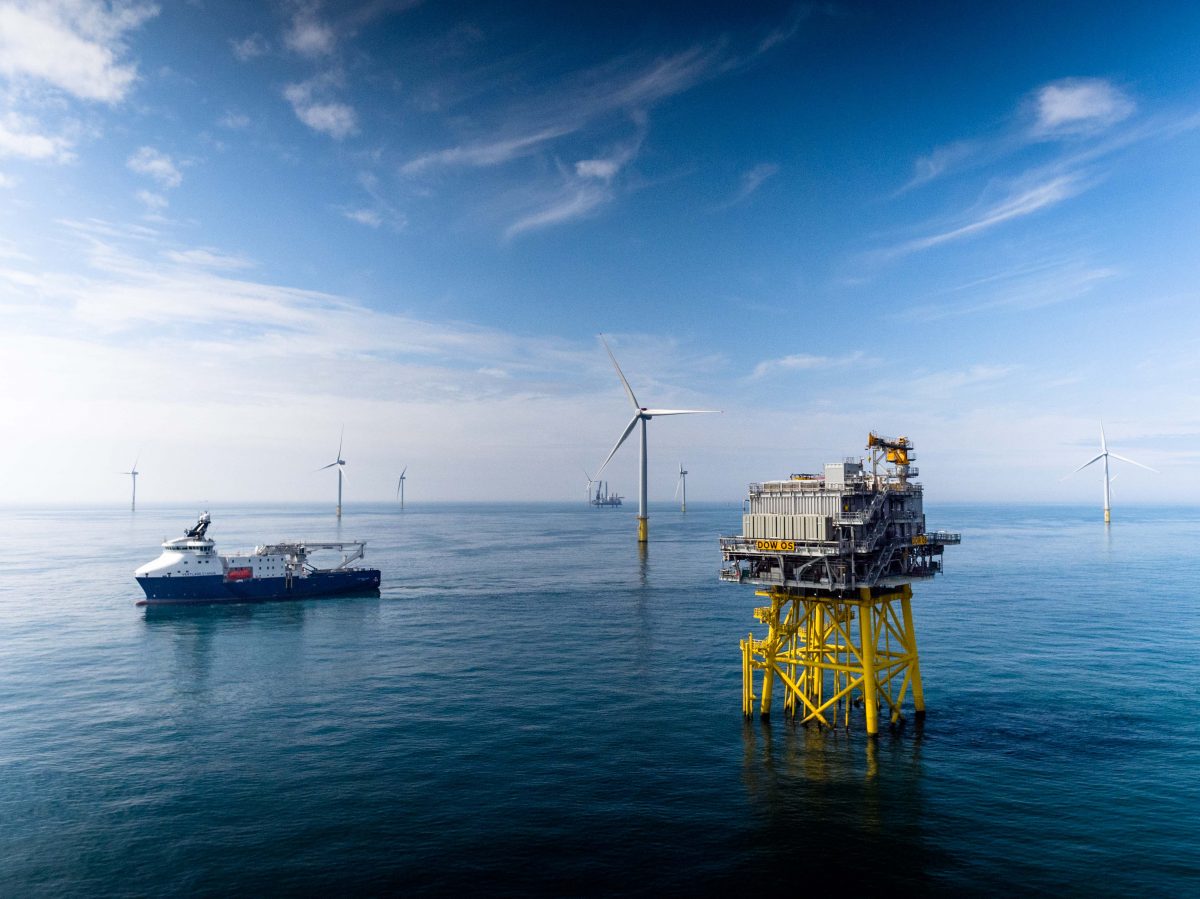
© Jan Arne Wold – Woldcam – Statoil
Together with a heave compensated gangway for personnel transfer between the vessel and wind turbines, as well as an accommodation module, PALFINGER MARINE’s new AHC crane played a key role in Vestland Cygnus’ transformation into a “walk-to-work” vessel contracted by Statoil for work on the Dudgeon wind farm on the UK continental shelf – where the ship is currently operating.
WE CHOSE THE PALFINGER MARINE CRANE BECAUSE OF ITS LOW WEIGHT IN COMBINATION WITH THE LOW CENTER OF GRAVITY, WHICH MAKES IT POSSIBLE TO INSTALL A LARGER CRANE THAN ORIGINALLY PLANNED.
Hans Martin Gravdal, ship-owner and owner of Norside
A COMPLETE PACKAGE DELIVERED
“We have a long-standing reputation for delivering robust and reliable offshore equipment in close cooperation with the customer. We have put a lot of effort in making the design as optimized as possible when it comes to weight and operational features. This played a key part in winning this order”, says Jan Silgjerd, Head of Global Marine Application Engineering at PALFINGER. With the addition of the 100 tons AHC crane onboard Vestland Cygnus, the vessel is now equipped with a complete deck equipment package from PALFINGER MARINE. The package further includes smaller marine cranes, a complete winch package with anchor and mooring winches, as well as lifeboats. “This major delivery once again proves PALFINGER MARINE as the complete deck equipment supplier for the maritime industries. Having all equipment from one supplier and getting access to the industry’s largest global service network means added value for our clients, as it saves them time, resources and service visits”, Jan states.
Active Heave Compensation – A Challenging Design Task
“The development was carried out with a maximum focus on safety for cargo, equipment, personnel and environment. All the latest technology and smart system design is used to optimise the crane’s performance. The reduction in crane tip movement with up to 98 percent, place PALFINGER MARINE’s AHC cranes in the absolute top level with regards to compensating performance”, says Senior Mechanical Engineer Morten Søvik. He was PALFINGER MARINE’s designer responsible for the AHC crane, leading the expert team of engineers through the development process.
HOW MUCH CAN BE PLACED INSIDE
One of the design challenges was to ensure that the crane got a low weight and low center of gravity, as this gives the crane high lifting capacity compared to its weight – making it possible to increase the loading capacity on the vessel deck. “To achieve the low center of gravity for the crane we needed to place as many of the components as possible inside the crane column/slewing house and at the same time allow for access to all points of maintenance, inspection and service. This turned out to be a major challenge, but we managed to solve it in the end”, says Morten.
PROVIDING FOR THE OPERATOR
Another key focus during the entire design phase was to make the operator environment as optimal as possible with regards to ergonomics and easy to use systems. The result was a comfortable state-of-the-art operator cabin with superior control system and operator screen showing interactive load charts, mode selections, a comprehensive monitoring system and automatic detection of component maintenance needs – allowing the operator to focus entirely on executing the crane operations safely and precisely.
Curious for more project updates? Check out our story including image and video material of the transport of our AHC crane from our production site to the harbor.