Last Updated on May 9, 2022 by PALFINGER
Digital transformation has been a buzzword for decades, but only very few companies have made significant strides forward in this exciting and disruptive field. PALFINGER and Optilift are two such companies – and strategic partners. As part of our Marine Meetup series, we sat down with Torbjørn Engedal, Chief Technology Officer at Optilift, to discuss his view of digital transformation, his exciting career, and his perception of our industry’s future.
Which major development in digitization/artificial intelligence in the maritime and offshore industry have you witnessed in the past decade(s) – or even actively been part of in your capacity as Chief Technology Officer at Optilift?
Since around 2005, the offshore oil and gas industry has placed an increasing emphasis on digital and automation solutions for drilling and well activities. Additionally, several production processes have been changed to allow monitoring and control from onshore control rooms. Also, in the last few years, drones have taken over more inspection work offshore. Some operators have started experimenting with autonomous legged or wheeled robots such as ARGOS by Total. To name another example, Equinor experimented with delivery of goods from onshore to offshore by unmanned helicopter in 2020 and eventually entered a contract for commercial cargo delivery in December 2021.
Starting in 2010, we at Optilift have reflected on the fact that lifting and load handling are a part of the offshore industry lagging behind in terms of innovation. With our competence in artificial intelligence and computer vision, it was clear to us that we could contribute to improvements in these areas. In early 2014, we launched our first commercial product called the Motion Reporter. This was (and is) a revolutionary solution that only requires crane instrumentation to perform non-contact measurement of all relative motions between crane and vessel.
From late 2017 on, Aker BP challenged Optilift to set up sole remote operated offshore lifting operations, controlled from an onshore operation center. A critical aspect was to ensure safe operations in situations where the network link may be unstable, delayed, or even disconnected. Such a solution requires advanced perception of the environment, relying heavily on AI and computer vision. The remote-controlled and autonomous solution developed by Optilift was first tested on a full-size crane in Egersund, Norway, in 2021. It involved PALFINGER’s fully electric Wire Luffing Lattice Boom Crane to be provided to Aker BP’s Valhall field. The plan is to continue testing and qualifying the technology offshore at Valhall with the same crane from early 2022 onwards.
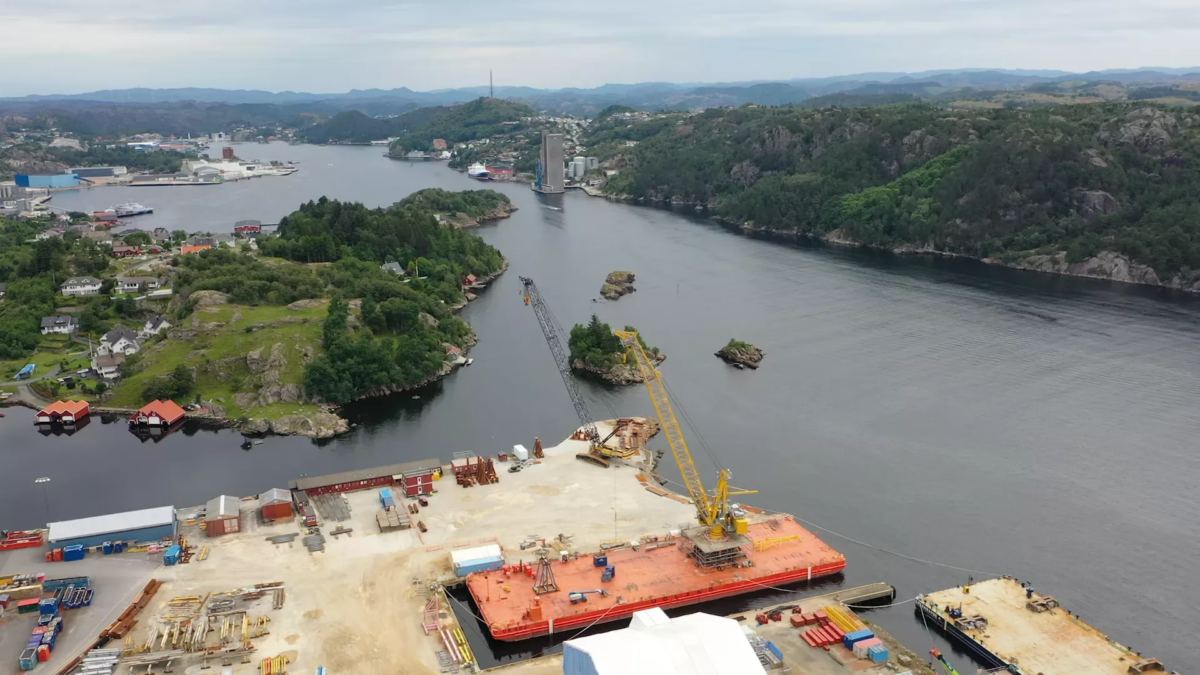
Full-size test of remote crane control system in Egersund, Norway. © Optilift
“The future is digital” has become a commonplace thing to say. How will the shift to “digital handling solutions” affect offshore operations and the working environment, and in which maritime industries do you see the greatest future potential for this shift?
“Digital” has, in fact, been around for a few decades already, and some industries, such as the automotive industry, have come far in this respect. However, many other industries, including marine and offshore handling operations, have not progressed as far. These fields face a few additional challenges compared to factory floors, such as unpredictable and uncontrollable events as well as rough offshore conditions. Digital systems in such industries require more intelligence and robustness.
When the marine and offshore industry fully embraces the use of digital, remote-controlled, and autonomous solutions, the safety and efficiency of operations may well drastically increase.
The ability to move people away from dangerous sites and working conditions is one of the main drivers for remote and autonomous control. However, it is also expected to yield huge cost-savings, particularly for operations that traditionally require either very calm weather conditions, large crews and facilities, or highly repetitive tasks that can be performed remotely with new digital tools. Both offshore wind and oil & gas operations have significant potential in this respect, especially in terms of load handling.
Optilift’s mission is to improve safety, efficiency, and logistics flow in cargo handling both onshore and offshore. How does your background and professional expertise enable you to contribute to this mission and which challenges do you face when tackling a new project?
Optilift solutions have been developed, tested, and deployed in close collaboration with operators in the oil and gas industry. These have helped the team identify the needs and challenges in lifting and logistics over the last 10 years, and we have combined these findings with our core technology development competence in computer vision, artificial intelligence, and robotics to develop robust and efficient products. The combination of hardware and software development, coupled with 10 years of data and 7 years of our hardware being operational offshore, has given us unique insight. It has enabled us to keep developing advanced tools and suggest improved ways of working. This includes digital tools for planning and lifting, remote control, and autonomy.
Optilift and PALFINGER already share some joint project history. One of them is our project involving remote lifting using Auto-Hook with the new 60T fully electric Wire Luffing Lattice Boom Crane at Valhall. What makes this specific project outstanding?
Yes, this is a project of strategic importance for Optilift in view of our mission. The combination of an agile and innovative end customer with their own mechanical solutions to remove personnel from the load decks (Aker BP) and a highly competent machine builder (PALFINGER), coupled with the team and technology of Optilift, results in a unique opportunity to develop, test, and qualify advanced technology in a safe and efficient manner at an actual offshore site.
In this project, each party brings their unique expertise together to solve challenges and reach the end goal. The focus of the project is to ensure safe, robust, and efficient remote control with assistance systems that can be linked with autonomous lifting operations. The main challenge is the large distance from the boom tip to the supply vessel when automatically hooking on cargo while the vessel is moving, and where environmental conditions may be harsh and changing. To solve this challenge, perception and robotic control technology – in many ways similar to technology for self-driving cars – is being developed and tested on the 60T fully electric PALFINGER Wire Luffing Lattice Boom Crane.
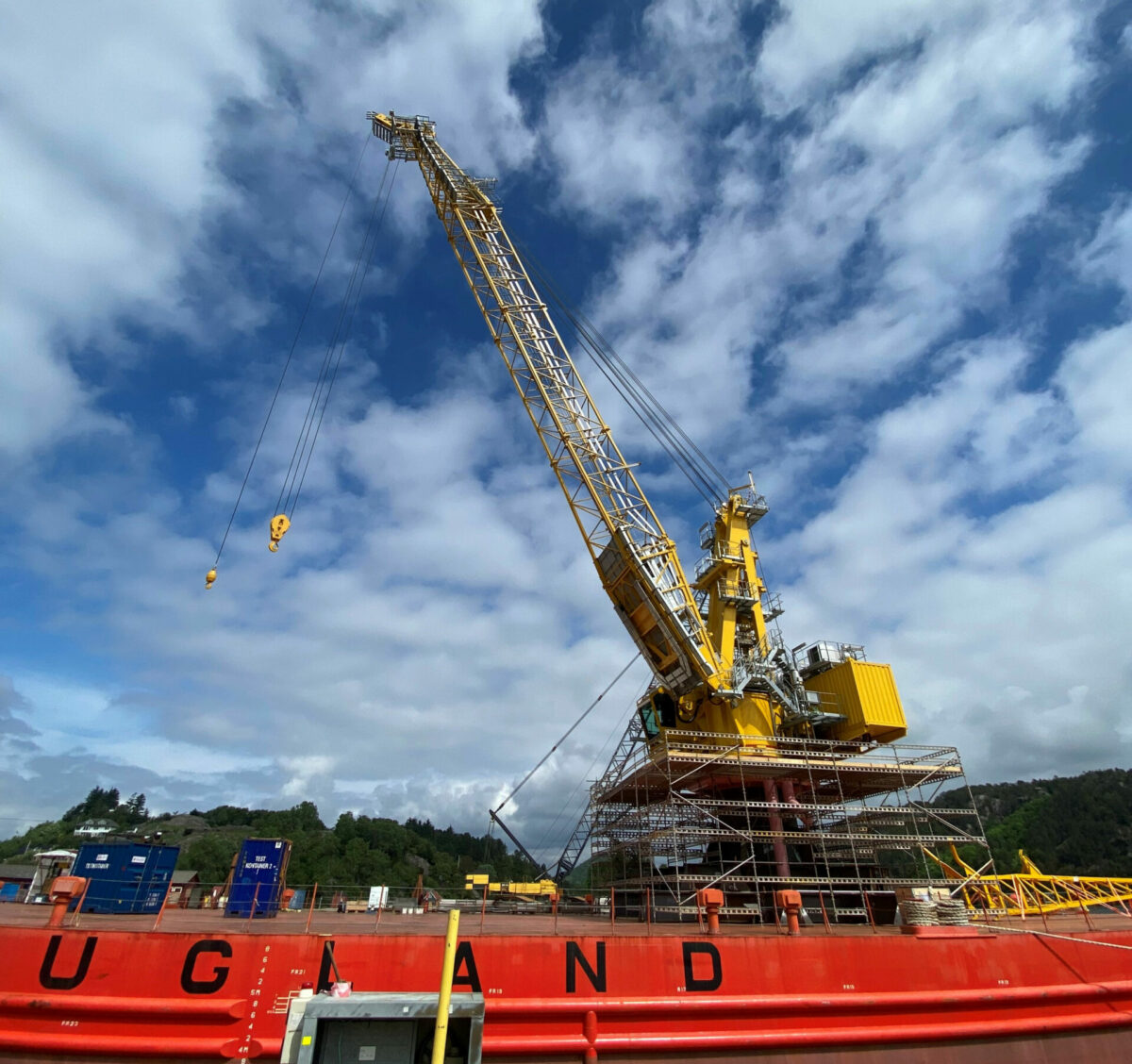
PALFINGER Wire Luffing Lattice Boom Crane, quipped with Optilift´s advanced sensor system and software, during tests in Egersund, Norway.
If you had to name one of your most – or the most – outstanding project(s) of your career so far, which one would it be and what makes it so special?
I would say what is about to become the realization of the long-term ambitions we have had for Optilift: to be the key enabler of technology to perform autonomous offshore crane operations. It is the most ambitious and outstanding project I have been part of. But it is important to mention that this end solution consists of several modules that have been built up as separate projects and products developed over the years by Optilift.
Furthermore, we are currently working on a research project led by the parent company of Optilift. The aim is to further the development of digital and autonomous offshore crane operations to land-side equipment, with targeted load handling at terminals. It involves cranes, forklifts, reach stackers, and other load handling machines. The project’s goal is to allow machines to operate, interconnect, and collaborate in an autonomous manner. The solution will simply be retrofitted to the machines, integrating our software into the respective control systems.
It is hard not to become excited by the future when listening to Torbjørn talk about what lies ahead. Naturally, PALFINGER is proud to play an active role in shaping this future with our partners. This is what the Marine Meetup series is all about – shining a light on how exciting the maritime and offshore industry really is.